Testing of advanced solutions for digital grinding, advanced forming, machining and multitasking, micromachining, digitising and connectivity, and other processes
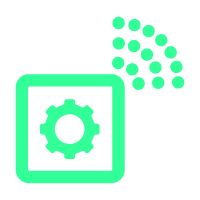
The Smart and Connected Machines focus area brings together a series of technological assets for companies, enabling them to carry out trial, testing, development, demonstration and training activities on the most established types of machines and manufacturing processes in the Basque industrial sector.
This focus area therefore provides specialised assets (machines, test benches, verification and test equipment) for conventional machining processes, multifunctional machining, process hybridisation, grinding and finishing processes, micromachining and precision processes, forming and joining processes, as well as software assets for testing aspects related to connectivity, digitisation and advanced control strategies.
Application areas
12 organisations and more than 42 assets to support:
Finishing
Technologies Machining
and Multitasking Precision and
Micro Machining Digitalization
and Conectivity Other processes
Advanced Forming
Finishing
Technologies
and Multitasking
Micro Machining
and Conectivity
View assets of node
Smart and connected machines
Contact your liaison
This is our expert in Smart and connected machines and will be in charge of assessing your needs.
Ander Azkarate
IDEKO
aazcarate@ideko.es
943 74 80 00